螺纹连续指螺纹在结构或制造过程中,其牙型、间距等特征沿轴线无间断地重复延伸。
螺纹连续的奥秘与意义
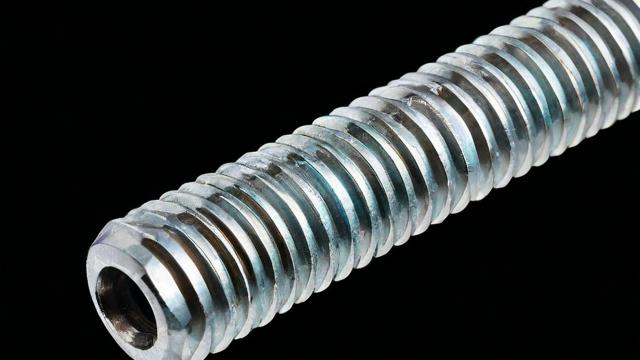
在金属加工、机械制造以及众多工业领域中,“螺纹连续”这一概念频繁出现,它看似简单,实则蕴含着丰富的技术内涵与重要意义,对于非专业人士而言,初次接触可能会觉得有些晦涩难懂,但深入了解后,会发现其在保障产品质量、提升设备性能等方面发挥着关键作用。
从字面意义理解,螺纹连续指的是螺纹在加工成型后,其牙型轮廓沿着螺旋线方向不间断、无缺失地延伸,以常见的圆柱螺纹为例,正常的螺纹应该是一圈接着一圈,如同链条般紧密相连,每个牙型的顶部与底部、两侧都完整呈现,不存在突然中断或缺损的情况,这意味着在微观视角下,螺纹的线条流畅,从起始端到终止端一气呵成,没有出现因加工失误、材料缺陷等导致的螺纹断裂、缺牙等问题。
在实际应用中,螺纹连续的重要性不容小觑,于机械装配环节,连续的螺纹能够确保螺栓与螺母之间的完美配合,当拧紧螺母时,螺栓上的连续螺纹会与螺母内的螺纹均匀受力,力能顺着完整的螺纹结构平稳传递,从而实现紧固效果的最大化,倘若螺纹不连续,存在局部缺失,那么在承受外力时,该部位就无法有效分散应力,极易形成应力集中点,随着使用时间推移或负荷增大,这些薄弱处可能率先发生变形、松动,甚至引发整个连接结构的失效,轻则影响设备正常运行,重则造成安全事故,比如在航空航天领域,零部件连接的可靠性关乎飞行安全,一丝螺纹的瑕疵都可能导致灾难性后果;在汽车制造中,发动机缸体等关键部件的螺纹连接若出问题,会影响动力传输稳定性,降低车辆安全性与使用寿命。
从加工工艺角度剖析,达成螺纹连续并非易事,它对加工设备、刀具精度以及操作工人技艺都有严苛要求,在车削螺纹时,车床的精度至关重要,机床丝杠的精度误差必须控制在极小范围内,因为丝杠的运动直接决定螺纹的导程与螺距准确性,一旦丝杠有细微偏差,加工出的螺纹就可能产生错牙、螺距不等现象,破坏螺纹连续性,刀具方面,螺纹车刀的刃口要锋利且几何形状精准,磨损过度的刀具切削出的螺纹表面粗糙、牙型不规整,容易出现毛刺、缺牙等缺陷,阻断螺纹连贯性,操作工人的经验与专注度也不可或缺,合适的切削参数选择、稳定的进刀手法,都是保障螺纹连续的关键因素,进刀速度过快,易造成刀具崩刃、螺纹撕裂;进刀过慢,又可能使工件材料因挤压过热而变形,同样影响螺纹质量。
检测螺纹是否连续,有着一套严谨的方法体系,目视检测是初步手段,借助高倍放大镜或光学显微镜,可清晰观察螺纹表面有无肉眼可见的断牙、裂纹等明显缺陷,但对于微小的不连续情况,还需借助专业量具,螺纹规是常用工具,它能精确匹配标准螺纹牙型,贴合被测螺纹,若螺纹规与螺纹不能完全吻合,存在间隙或阻滞,说明螺纹牙型可能有变形、不连续问题,三针测量法也较为常见,将三根直径已知的精密量针放置在螺纹沟槽内,用千分尺测量出三针外侧距离,通过特定公式计算得出螺纹中径等参数,间接判断螺纹完整性,若计算出的数值偏差超出公差范围,意味着螺纹可能存在不连续隐患,随着科技发展,无损检测技术如 X 射线探伤、超声波检测等也逐渐应用于螺纹检测,它们能穿透材料内部,发现隐藏在表层下的螺纹缺陷,像一些因铸造工艺导致的内部砂眼、气孔影响螺纹连续性,传统方法难察觉,而这些先进检测手段却能精准识别。
在工业生产标准化进程中,螺纹连续是衡量产品质量的关键指标之一,各类行业标准对不同用途螺纹的连续性都有明确规定,例如在压力容器制造领域,法兰连接处的螺纹必须连续且无任何缺陷,以确保密封性能,防止介质泄漏;在建筑行业,钢结构连接螺栓的螺纹连续性直接影响结构强度与抗震性能,不符合标准的螺纹产品严禁使用,这些标准规范不仅约束生产企业保证产品质量,也为质量监管部门提供了明确依据,通过严格抽检,将不合格产品拒之市场门外,维护行业健康有序发展。
于产品研发创新层面,追求螺纹连续也推动技术不断进步,科研人员为解决复杂工况下螺纹易损坏、难保证连续的问题,研发新型合金材料,提升材料韧性与抗疲劳性,使螺纹在极端温度、压力、摩擦环境下依旧保持完整;优化加工工艺,如采用高精度数控加工中心、多轴联动技术,结合智能编程,让螺纹加工精度迈向新台阶;开发自动化检测设备,利用机器视觉、人工智能算法实时监测螺纹加工过程,即时发现并纠正可能影响螺纹连续的问题,极大提高生产效率与产品良品率。
螺纹连续虽是一个微观层面的技术细节,却如同大厦基石,支撑起整个制造业的质量大厦,它是机械精密性的直观体现,是安全可靠运行的坚实保障,更是工业文明持续进步的有力见证,无论是老牌制造企业坚守品质底线,还是新兴创业公司开拓市场版图,对螺纹连续的执着追求都不应懈怠,因为这一小小的螺纹背后,承载的是行业发展重任,关乎产品生死存亡,只有牢牢把控螺纹连续这一关,才能在激烈的市场竞争浪潮中稳立潮头,驶向制造业的远方。